Common Causes Of Air Compression Failure And How To Fix Them
Publish Date : 02-12-2024
Views : 1331
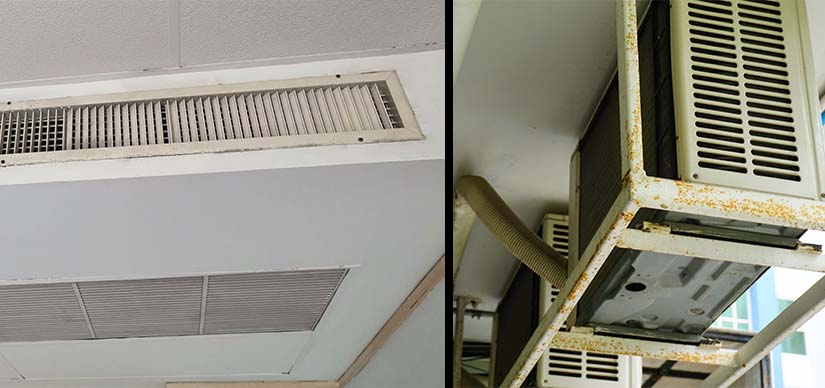
San Diego's semi-arid climate is renowned for its consistently mild and dry weather. In contrast to the winter, which is cool and mostly dry with average high temperatures in the mid to upper 60s Fahrenheit, the summers are warm and dry with average high temperatures in the mid to upper 70s Fahrenheit (roughly 24-26 degrees Celsius) (around 18-20 degrees Celsius). To feel comfortable during summer times, most San Diegans use the air conditioning system in their homes and businesses. However, one of the most important components of an AC system - the compressor - might sometimes fail. In such a case, you are left with no option but to call an air conditioning repair service in San Diego. But before calling for an emergency AC repair in San Diego, what are some common causes of air compression failure and can you fix them yourself? Read on as these questions are discussed below.
The Compressor Won't Turn On or Turn Off
The inability of air compressors to turn on or off is one of the most frequent problems with them. A defective motor, a problematic pressure switch, or an electrical issue are just a few possible causes. Your operations may be affected and delayed if your compressor won't start. Similarly, if it won't shut off, it may result in equipment failure, overheating, and other problems. Try these fixes to see if they help with the compressor not turning on or off:Check the power supply and electrical connections
Make sure the power supply is sufficient and operating properly. Make sure the electrical connections are secure and not corroded, damaged, or loose. Replace any damaged connections and tighten any that are loose.Inspect the pressure switch
According to the pressure levels in the tank, the pressure switch is in charge of turning the compressor on and off. If it's broken, it might not activate or deactivate the compressor as intended. Look for any signs of wear or damage on the switch, and replace it if necessary.Replace the motor
The compressor might not start or stop as intended if the motor is damaged or burned out. Look for any signs of wear or damage on the motor, and replace it if necessary.Issues with Electrical Motor and Power
Problems with the electrical motor and power are another frequent reason for air compressor failure. The motor drives the compressor pump, and if it breaks down, the compressor won't operate properly. Possible reasons for problems with the electrical motor and power include the following:Electrical overload
The motor and compressor may become damaged as a result of an electrical overload. Make sure the electrical circuit can handle the power demands of the motor.Faulty start capacitor
The start capacitor provides the initial power boost to the motor, allowing it to start. If the capacitor is faulty, the motor won't start properly.Worn-out motor brushes
The motor brushes are responsible for delivering power to the motor. Over time, they can wear out, causing the motor to malfunction.How to fix issues with electrical motors and power:
- Check the electrical circuit and ensure that it can handle the motor's power requirements.
- Replace a faulty start capacitor.
- Replace worn-out motor brushes.
- Consider hiring an emergency AC repair in San Diego for professional assistance.
Compressor Vibrations and Noise
A common cause of air compression failure can also be compressor noise and vibration. While excessive noise can disrupt operations and be uncomfortable for workers, vibrations can harm the compressor and adjacent machinery. Here are a few possible reasons why a compressor might vibrate or make noise:Imbalanced components
Vibrations and noise may be produced by the components of the compressor if they are out of balance. This may be brought on by pulley damage, bent crankshafts, or worn-out bearings.Loose mounting bolts
If the mounting bolts are loose, it can cause the compressor to vibrate excessively.Clogged air filter
A clogged air filter can restrict airflow, causing the compressor to work harder and vibrate more.How to fix compressor vibrations and noise:
- Inspect the compressor's components and replace any worn-out or damaged parts.
- Tighten any loose mounting bolts.
- Replace the air filter if it is clogged.
- Consider installing anti-vibration pads or mounts to reduce vibrations.
- Consider hiring an air conditioning repair service in San Diego for professional assistance.
Also Read: 5 Causes Of Air Conditioner Noise And How To Fix Them
Air Leakages
Air leakage is another frequent reason for air compression failure. The compressor may have to work harder as a result of air leaks, which could result in higher energy costs and lower efficiency. Additionally, they might harm the compressor and adjoining machinery.Here are some potential causes of air leakages:
Faulty valves
Faulty inlet and discharge valves can cause air to leak out of the compressor.Damaged seals
Damaged seals can cause air to leak out of the compressor.Loose fittings
Loose fittings can cause air to escape from the compressor.Cracked or damaged hoses
Cracked or damaged hoses can allow air to escape from the compressor.How to fix air leaks:
- Identify the source of the leak by using a leak detection solution or a soapy water solution.
- Tighten any loose fittings.
- Replace any damaged or worn-out valves, seals, or hoses.
- Consider installing a pressure regulator to reduce the risk of future leaks.
- Consider hiring an air conditioning repair service in San Diego for professional assistance.
Problems with Flow and Pressure
Failure of air compression can also be brought on by issues with flow and pressure. These problems may affect how well the compressor functions as well as the tools and equipment it drives. The following are some typical causes of flow and pressure issues:Clogged air filters
Clogged air filters can restrict the flow of air and decrease the pressure output.Dirty or damaged compressor components
Dirty or damaged compressor components, such as the intake valve or pressure switch, can restrict the flow of air and decrease the pressure output.Worn-out compressor parts
Worn-out compressor parts, such as the piston rings or valves, can cause a drop in pressure and flow.Improper installation
An improperly installed compressor can cause flow and pressure problems.How to fix flow and pressure problems:
- Air filter cleaning or replacement.
- Clean or replace any dirty or damaged compressor components.
- Replace any worn-out compressor parts.
- Ensure that the compressor is properly installed and connected.
- Consider installing a larger or more efficient compressor if the current one is unable to meet the required flow and pressure demands.
Hot Emissions at Maximum
It's vital to fix the problem right away when a compressor is producing hot air at full capacity. The compressor may become damaged from overheating, which would have a negative effect on its operation. Consequently, it is imperative to identify and address the problem as soon as possible.Overheating
Overheating can be caused by a lack of proper airflow, a malfunctioning temperature sensor, or a faulty cooling fan.Low oil level
Low oil levels can cause the compressor to overheat and emit hot air.Malfunctioning pressure switch
A malfunctioning pressure switch can cause the compressor to run at maximum capacity, leading to overheating and hot emissions.How to fix hot emissions:
- Ensure that the compressor has proper ventilation and airflow.
- Verify the oil level and add more if required.
- Inspect the temperature sensor and replace it if it is malfunctioning.
- Replace any faulty cooling fans or pressure switches.
- Consider installing an external cooling system or upgrading the current system to prevent overheating.